13 Proven Ways to Protect Bearings from Damage and Common Failures.
- Masa Technologies
- May 10
- 5 min read
Bearings are the unsung heroes in a vast array of rotating equipment, from small electric motors to massive industrial turbines and machinery. They perform the critical task of reducing friction, supporting loads, and enabling smooth, efficient motion. However, like any mechanical component, bearings are subject to wear and can fail prematurely if not properly maintained.
Neglecting bearing maintenance can have significant consequences. Sources indicate that poor bearing maintenance is a leading cause of equipment failures. Proper care can extend bearing life significantly. Conversely, early bearing failures can lead to unexpected downtime, costly repairs, reduced productivity, and potential safety hazards.
Understanding the common bearing failure reasons and implementing effective strategies for preventing bearing damage are crucial for maintenance personnel and engineers.
Common Bearing Failure Reasons:
Bearings may fail earlier than their expected rolling fatigue life primarily due to inadequate handling or maintenance. Identifying the root cause of failure is essential to prevent recurrence. Some frequent bearing failure reasons include:
Improper Lubrication This is one of the most common causes. Using the incorrect type of lubricant, or applying too much or too little, can cause overheating and premature wear. Proper lubrication reduces friction, dissipates heat, prevents corrosion, and seals out contaminants. The correct lubricant depends on the bearing selection and its application, considering factors like environmental conditions, temperature, speed, and load.
Contamination Particles, even those invisible to the naked eye, can significantly reduce bearing life by causing abrasion and fatigue. Dirt, dust, debris, and water can enter the bearing's sensitive components. Moisture and water presence can lead to rust and corrosion, causing premature bearing fatigue.
Misalignment Every bearing has an alignment tolerance. Operating beyond this tolerance will cause damage. Misalignment can also indicate issues elsewhere in the machine.
Improper Installation Incorrect installation techniques can damage a bearing before it even begins operation. Applying force to the wrong ring, using direct hammering, or failing to follow manufacturer guidelines can lead to dents, cracks, scratches, and misalignment. Driving a tapered bore bearing too far onto a taper can cause improper interference and potential inner ring fracture or seizure.
Excessive or Incorrect Loading Bearings are designed to handle specific load types and magnitudes. Operating outside these specified parameters can dramatically shorten bearing life. Excessive loads, including axial loads or shock loads while stationary or during mounting, can cause damage like flaking. Overloading can also cause lubricant overheating and thinning, leading to component contact.
Operating Temperatures Outside the Bearing's Range Exceeding the maximum permitted temperature can permanently deform or soften the bearing steel, reducing its load carrying capacity and leading to failure. Discoloration of bearing components can indicate overheating.
Wear and Fatigue While rolling fatigue is a natural endpoint for a bearing's life, early fatigue can result from inadequate handling or maintenance. Accelerated wear can occur under continuous high-temperature operation. Visible signs include flaking, peeling, spalling, smearing, wear patterns, indentations, chipping, cracking, rust, corrosion, seizing, fretting, electrical pitting, and damage to cages.
Improper Handling and Storage Bearings are precision components that should be handled and stored correctly to prevent contamination and damage. Storing them in a clean, dry environment with intact packaging is recommended. Dropped or mishandled bearings may have hidden damage and should not be installed.
Other factors contributing to bearing failure include neglecting regular inspections, reusing damaged bearings, failing to address the root causes of identified issues, using incorrect or low-quality replacement bearings, and using improper servicing techniques or tools.

Preventing Bearing Damage: Essential Strategies
Implementing a comprehensive and proactive maintenance program is key to preventing bearing damage and maximising bearing lifespan. Here are proven strategies based on the sources:
Implement a Strategic Maintenance Plan Develop a schedule for preventive inspections. A proactive strategy like predictive maintenance, which involves the ongoing analysis of machine data, helps detect potential issues early and allows maintenance to be planned or even avoided, reducing unplanned downtime.
Handle and Store Bearings with Care Treat bearings as precision components. Store them horizontally in a clean, dry environment in their original packaging. Prevent exposure to airborne contaminants. Wear gloves when handling to prevent corrosion from perspiration. Never strike a bearing directly or apply force to the wrong ring during handling or installation.
Prioritise Proper Lubrication Follow a strict lubrication schedule. Use the correct type and amount of lubricant specified for the bearing and its application. Lubricants serve as a barrier, prevent wear, reduce heat, and seal against contaminants. Consider using water-resistant grease in damp environments. Automatic lubrication systems can ensure consistent, correct lubrication.
Master Proper Installation Techniques Careful attention to installation procedures is crucial. Read the manufacturer's manual for specific requirements. Use the correct tools, such as bearing fitting tool kits, induction heaters (never open flame), hydraulic nuts, or oil injection kits. Ensure mating parts (shaft, housing) are clean and within dimensional specification. Check and adjust radial internal clearance during mounting, especially for tapered bores, verifying with feeler gauges. After mounting, check that the outer ring and shaft rotate easily by hand.
Control Contamination Keep bearings and their surrounding areas clean. Prevent dust and dirt entry. Implement effective sealing solutions, choosing the right seal type (contact, non-contact, bearing isolators) based on operating conditions and contamination risks. Regularly inspect and maintain seals. Clean bearings using appropriate methods and solvents, applying anti-corrosion protection immediately after.
Check for Misalignment Periodically Verify alignment as a core part of maintenance. Alignment and balance are not "set and forget" procedures. Rotating equipment vibration analysis can identify symptoms of misalignment early.
Manage Loads Effectively Understand your bearing's dynamic and static load ratings. Ensure operating conditions (load, speed, temperature) are within the bearing's specified limits. Use the correct bearing type (radial vs. axial) for the load direction.
Monitor Bearing Health (Predictive Maintenance) Utilise techniques like vibration analysis, temperature monitoring, and operating sound checks to detect early signs of degradation or issues. Changes in these parameters often appear before visible damage or operational disruptions. Proactive monitoring helps reduce unexpected downtime. Smart bearings with sensors can provide real-time data.
Conduct Regular Inspections Schedule routine visual inspections for signs of wear, corrosion, damage, or contamination. Inspect seals and shields. For internal condition checks, this may require dismounting.
Know When to Replace Bearings Bearings have a finite lifespan and must be replaced when they reach the end of their useful life or show signs of significant damage or distress. Watch for abnormal noise, increased vibration, or overheating. Regular inspection helps predict when replacement will be necessary. If internal components like rings or balls are damaged, replacement is usually unavoidable.
Choose Quality Replacements When replacing a bearing, choose one that is identical or superior in quality to the original. Select the appropriate type, material, and design for the specific application's load, speed, and environmental conditions. Use a reputable supplier. Avoid using standard bearings where a special design is required.
Ensure Proper Training Train maintenance personnel on proper bearing inspection, cleaning, handling, and installation procedures. This ensures that bearings are maintained correctly, and issues are identified and resolved quickly.
Use the Proper Tools Always use specialised tools designed for bearing mounting and dismounting to minimise the risk of damage.
Adhering to safety standards and using appropriate Personal Protective Equipment (PPE) during maintenance tasks is also essential.
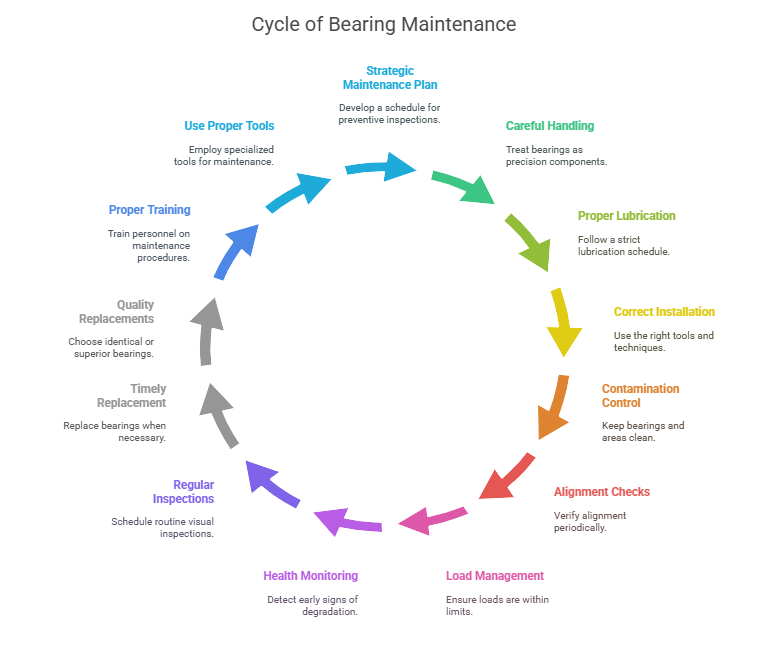
Conclusion
Understanding the basics of bearing maintenance, including the common bearing failure reasons and best practices for preventing bearing damage, is fundamental for anyone involved with rotating equipment. Implementing a comprehensive, proactive maintenance program that includes proper handling, lubrication, installation, monitoring, and timely replacement is not just about extending bearing life; it's about ensuring the reliable and efficient performance of your machinery, reducing downtime, cutting costs, and improving overall safety and productivity.
By integrating these strategies into your maintenance routine, you can significantly enhance equipment reliability and avoid the costly consequences of unexpected bearing failures.
Comments